Building a Chicken Plucker: Step-by-Step Guide
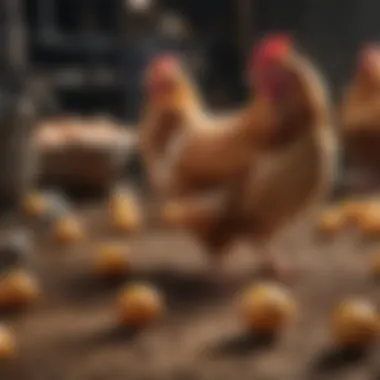
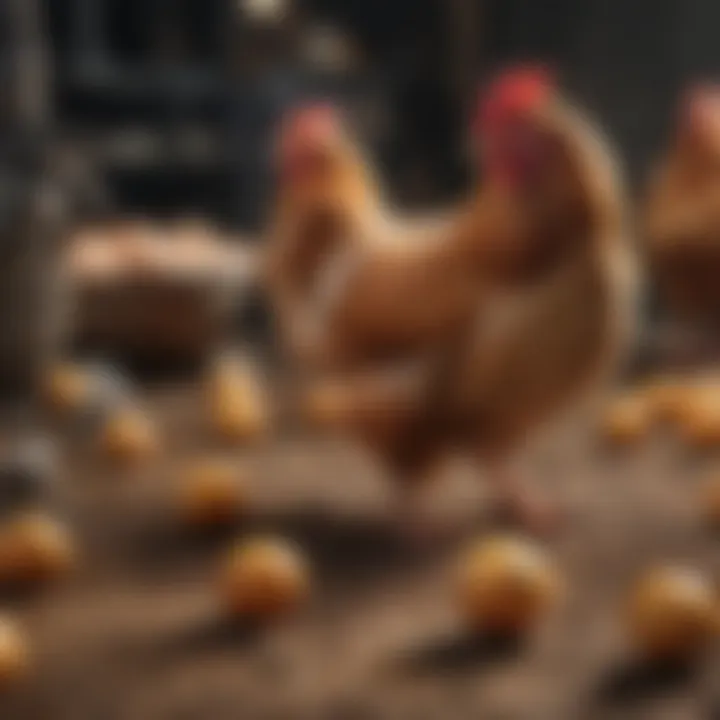
Intro
Building a chicken plucker is an essential undertaking for anyone involved in poultry processing. This guide delves into the intricate steps and components necessary for constructing your very own chicken plucker. It aims to equip both novice builders and seasoned individuals with the insights needed to venture into this project. The process not only enhances efficiency but also significantly simplifies the task of plucking, which is often seen as laborious.
As you navigate through this guide, expect detailed explanations of various designs, necessary materials, assembly methods, and maintenance practices. Additionally, insightful solutions to common challenges encountered during construction are provided. Understanding these aspects is crucial to ensure a successful build that caters to your specific needs in poultry processing.
Key Points to Discuss
The following sections will outline significant features related to building a chicken plucker, including:
- Detailed overview of essential components
- Variations in design that can improve functionality
- Step-by-step instructions for assembly
- Maintenance tips to ensure longevity
- Solutions to common construction problems
This comprehensive approach will enrich your understanding of poultry processing equipment and ensure a practical understanding of how to build and maintain an efficient chicken plucker.
Prologue to Chicken Pluckers
Understanding chicken pluckers is crucial for anyone involved in poultry processing, whether on a small homestead or in a larger farming environment. They play a fundamental role in expediting the plucking process, which traditionally was both labor-intensive and time-consuming. The adoption of chicken pluckers significantly enhances the efficiency and cleanliness of poultry preparation, making it an essential tool for serious poultry keepers.
Definition and Purpose of a Chicken Plucker
A chicken plucker is a machine designed to remove feathers from a chicken after it has been slaughtered. The primary purpose of this equipment is to automate the plucking process, reducing the need for manual labor. Without a plucker, removing feathers can take a considerable amount of time and human effort, which is not always feasible when processing several birds at once.
The machine operates by using rubber fingers that rotate rapidly. These fingers grip the feathers and pull them out efficiently without damaging the skin of the bird. By employing a chicken plucker, poultry processors can improve not only the speed of the operation but also its overall hygiene. Additionally, with a well-constructed plucker, one can achieve a cleaner final product with less waste.
Historical Context of Poultry Processing
Poultry processing has evolved significantly over the years. Historically, chickens were plucked manually, a process that dates back to ancient civilizations. Early farmers used simple tools like knives and their hands. This method was laborious and often led to inconsistent results. As populations grew and demand for poultry increased, the need for better methods became evident.
The late 19th and early 20th centuries marked the beginning of industrial poultry processing in the United States. During this time, various machines, including the first chicken pluckers, were developed. These innovations transformed the way poultry was processed, allowing for higher production rates. Modern chicken pluckers are now integral to both small-scale operations and large commercial processing plants. The historical shift from manual to automated processes highlights the importance of efficiency in poultry production and contributes to the current landscape of meat processing.
The advent of chicken pluckers has not only changed how poultry is processed but also has raised standards for hygiene and efficiency in the industry.
Understanding the Mechanism
Understanding the mechanism of a chicken plucker is crucial to the construction process. It allows builders to appreciate how each component interacts to achieve a significant task. Knowledge of the mechanism aids in troubleshooting and can enhance operational efficiency. This section will delve into how a chicken plucker functions and examine its key components.
How a Chicken Plucker Operates
A chicken plucker operates on a straightforward principle. It uses mechanical motion to remove feathers from a processed bird. The process begins with the chicken being placed in the drum, which rotates at a determined speed. As the drum turns, rubber fingers work in unison to grip and pull feathers from the skin. The combination of rotation and friction ensures that feathers are efficiently removed, thereby speeding up the processing time compared to manual methods.
Key Components of a Plucker
Drum
The drum is the heart of the plucker. It generally has a cylindrical shape and houses the rubber fingers. A well-designed drum contributes to the overall effectiveness of the plucking process. The key characteristic of the drum is its rotational speed. It is a vital aspect because the speed influences the efficiency of feather removal. A high-quality drum can handle various sizes of chickens, making it a popular choice in various settings.
One unique feature of the drum is its material construction, often made from stainless steel for durability. Stainless steel does not corrode, which is beneficial in the food industry. However, it can be heavier than other materials, which might complicate assembly.
Rubber Fingers
Rubber fingers are essential for the plucking effect. They play a crucial role in gripping and pulling feathers off the chicken's skin. The main characteristic of rubber fingers is their flexibility and durability. This makes them a favored choice for builders since they can conform to the contours of the chicken and effectively remove feathers without damaging the skin.
A unique aspect of rubber fingers is their varying lengths, which can be tailored to fit different designs. This variability can enhance the overall effectiveness of the plucking process; however, improper selection may lead to poor results in feather removal.
Drive System
The drive system is responsible for providing motion to the drum. It usually involves an electric motor connected to a belt or chain that spins the drum. The key characteristic of a solid drive system is its power. A powerful drive system allows for higher speeds, promoting better feather removal efficiency. This aspect is crucial for those looking to process large quantities of poultry.
One unique feature of modern drive systems is the option to control speed electronically. This flexibility allows users to adapt their approach based on the type and size of the chicken. However, this added technology can lead to increased costs in design and construction.
Frame Structure
The frame structure is foundational to the durability and stability of the entire plucker. It supports all the components and endures the stresses of operation. A key characteristic of a well-designed frame is its ability to absorb vibration while maintaining structural integrity. This is essential for safe and effective operation.
A unique feature of some frame structures is adjustability. Frames can be designed to accommodate different drum sizes or other components. This versatility can be beneficial for modifying the plucker for various tasks. On the downside, poorly constructed frames may lead to inadequate support, impacting the function of the whole machine.
In summary, understanding these key components is vital for effectively building and operating a chicken plucker. Each piece interacts to fulfill the main purpose of feather removal efficiently and cost-effectively.
Essential Materials and Tools
Building a chicken plucker is a rewarding endeavor, and selecting the right materials and tools is crucial for success. Understanding the importance of these elements can simplify the process and enhance the overall outcome of your project. Using high-quality materials not only ensures the durability of the plucker but also can significantly influence its efficiency in processing poultry.
The tools required for construction are equally important. The right tools make assembly smoother and enable precise adjustments. This guide aims to inform how to choose and use the essential materials and tools effectively.
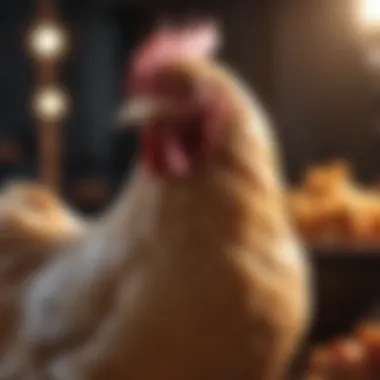
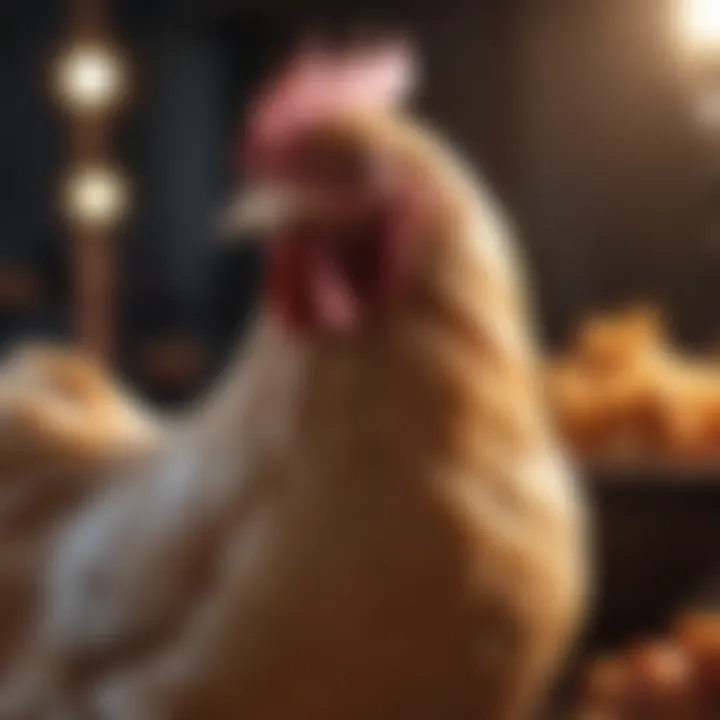
List of Materials Required
When constructing a chicken plucker, having the proper materials is fundamental. Below is a comprehensive list:
- Drum: This is where the plucking action occurs. It is typically made of metal or sturdy plastic to withstand wear.
- Rubber fingers: These components are crucial for plucking feathers effectively. They are usually durable and flexible to avoid damaging the skin.
- Motor: The motor provides the necessary power to rotate the drum. A reliable motor ensures consistent performance.
- Frame: A strong frame structure is necessary to house all components securely. It should be made from robust material like steel or aluminum.
- Wiring and connectors: These are essential for the electrical system, allowing for safe power delivery.
- Base: A stable base supports the entire structure. It is vital to ensure stability during operation.
These materials each have specific functions and contribute to the plucker's overall performance. Investing in quality materials can prevent future issues and enhance productivity.
Tools Needed for Construction
The right tools make a significant difference in how well and easily you can build a chicken plucker. Below are the tools you will need:
- Drill and drill bits: To make holes in various components for screws or bolts, a reliable drill is essential.
- Wrench set: A set of wrenches will help secure mechanical connections firmly.
- Screwdriver: A screwdriver is necessary for assembling different parts and ensuring everything is in place.
- Cutting tools: This can include saws for cutting the various materials to size.
- Measuring tape: Accurate measurements are crucial for a well-fitted chicken plucker.
- Safety gear: It is vital to have safety gloves, goggles, and masks to protect yourself during construction.
Having these tools ready before starting the project will help streamline the assembly process and minimize frustration. In addition, proper use of tools can significantly reduce the risk of injury.
Proper planning and preparation can enhance your building experience and lead to a more efficient chicken plucker.
Overall, the right selection of materials and tools is indispensable in the construction of a chicken plucker. Be attentive to the choices you make, as they directly affect the quality and efficiency of the final product.
Design Considerations
The design of a chicken plucker is crucial in ensuring efficiency and effectiveness during the poultry processing operation. A well-thought-out design not only maximizes performance but also enhances user experience. Selecting the right design can greatly influence the overall functionality, ease of use, and maintenance. It is essential to consider various aspects like available space, the expected volume of birds to be processed, and specific features that cater to your needs.
Different Types of Chicken Plucker Designs
Vertical Pluckers
Vertical pluckers are known for their upright design, which allows them to handle birds in a much more vertical alignment. This orientation aids in the gravity-assisted removal of feathers during the plucking process, which can enhance efficiency.
The key characteristic of vertical pluckers is their compact structure. This compactness makes them ideal for smaller spaces or for those who may only occasionally process chickens. One of the beneficial aspects is that they often require less power to operate compared to larger designs.
A unique feature of vertical pluckers is their ability to accommodate multiple birds at once, which is an advantage for homesteaders or small-scale processors. However, one drawback is that they may not be as effective for larger breeds or when handling larger volumes, making them less suitable for extensive commercial operations.
Horizontal Pluckers
Horizontal pluckers are designed to have a larger drum that rotates horizontally. This design allows for more space, making it easier to load multiple chickens at once. The capacity to handle more birds simultaneously is one major contribution to the efficiency of this design.
The significant characteristic of horizontal pluckers is their gentle plucking action. This action reduces the chance of damaging the skin of the birds, which is beneficial for quality. As a result, horizontal pluckers are popular among both home enthusiasts and some commercial processors.
A unique feature is the size and adaptability of these machines, often allowing for easy modification to meet various user needs. However, the larger size can be a disadvantage if space is limited, and they may come at a higher initial cost.
Portable Options
Portable chicken pluckers are gaining popularity due to their versatility and convenience. These models are usually lighter and compact, making them easy to transport and store. They can be used in various locations, which is an important factor for many users.
The key characteristic of portable options is their user-friendliness. They usually come with easy assembly features, allowing users to set them up quickly and start processing chickens without much hassle. This can be especially beneficial for small farms or backyard poultry keepers who require flexibility.
A unique feature of portable chicken pluckers is their design tailored for outdoor use. They often come with weather-resistant materials, making them ideal for users who may not have a dedicated indoor space. Nevertheless, a potential downside is limited capacity compared to static models, which means they may not be the best choice for larger operations requiring high throughput.
Choosing the Right Size
Selecting the appropriate size of the chicken plucker is vital for maximizing efficiency. Itโs important to assess the number of birds you plan to process at once and choose a size that matches those needs. Whether you require a smaller unit for personal use or a larger machine for commercial processing, understanding your requirements beforehand can lead to better performance and satisfaction.
Step-by-Step Assembly Instructions
Step-by-step assembly instructions are crucial for successfully building a chicken plucker. This process is designed to guide builders through each significant stage, ensuring a cohesive structure that functions effectively. A systematic approach minimizes errors, allows for better understanding of components, and fosters confidence in the builder.
Preparing Your Workspace
Creating an efficient workspace is essential before starting the assembly process. Clear the area of any unnecessary items to provide a clean and organized environment. This not only promotes safety but also enhances focus.
Ensure that tools are readily accessible and materials are sorted. This preparation saves time and reduces frustration during assembly. Additionally, good lighting and a sturdy table are necessary to prevent accidents and enable precise work.
Assembling the Drum
The drum is a core component of the chicken plucker. It is important to begin by securing the drum base to ensure stability. First, attach the drum sides to the base using bolts. Make sure they are tightened evenly to maintain the drum's shape.
Next, confirm that the drum is perfectly round. Any distortion can affect the plucking process. Once you're sure of the drum's integrity, proceed to affix the end caps. This step includes sealing any gaps to prevent feathers from escaping during operation.
Installing the Rubber Fingers
Rubber fingers play a vital role in the plucking mechanism. Installing them correctly is crucial for optimal performance. Start by evenly spacing the rubber fingers around the drum. Use an adhesive to secure them and ensure a firm grip. It is advisable to follow the manufacturer's specifications regarding finger length and quantity.
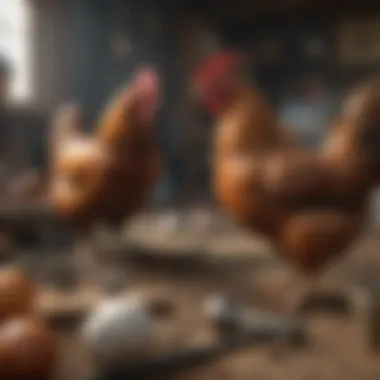
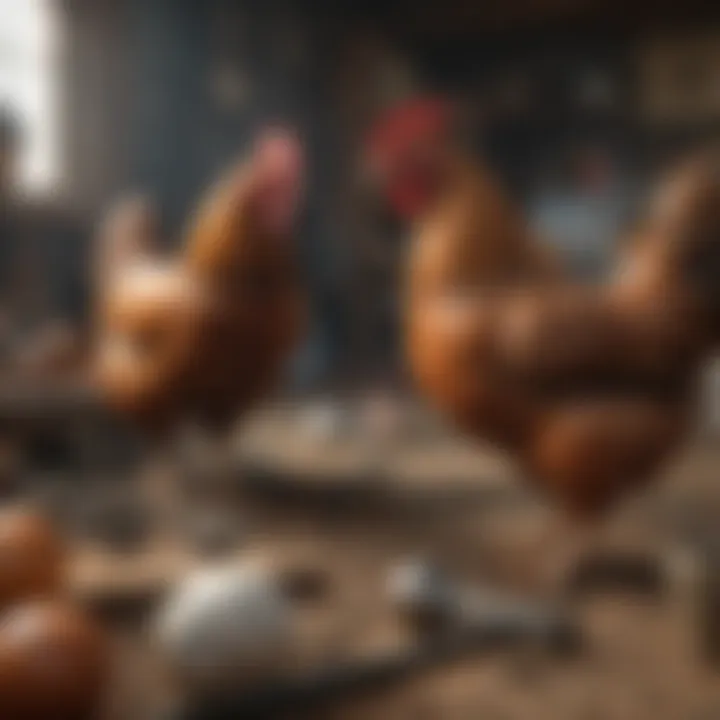
Checking the alignment of each rubber finger is key. They should not touch each other and should have enough flexibility to grasp feathers efficiently during operation. Incorrect installation can lead to unsatisfactory results.
Attaching the Drive System
The drive system provides the necessary movement to the drum, thus, it should be installed with care. Begin by positioning the motor and aligning it with the drum. Use a mounting bracket to secure the motor firmly in place.
Next, connect the motor to the drum using a belt or chain, depending on the design chosen. Ensure that the connection is secure but not overly tight, as this could lead to mechanical failure over time. After connecting, aim to adjust the tension according to specifications for smooth operation.
Final Frame Assembly
The final frame assembly brings together all components into a functional unit. Start by securing the drum assembly to the frame. Carefully line everything up, making sure the drum spins freely without obstruction. Ensure that all mounting points are correctly aligned.
After confirming alignment, finish by tightening all bolts and screws. This strengthens the overall structure and minimizes vibrations during use. Once complete, a visual check for loose connections or misalignments is advisable. This preparation helps ensure longevity and effective performance of the chicken plucker.
Testing and Calibration
Testing and calibration are critical components in the construction of a chicken plucker. These steps ensure that the machine operates at its maximum efficiency and effectiveness. Proper testing allows you to verify the functionality of each component, identifying any potential flaws before regular use. Calibration, on the other hand, optimizes the performance of the plucker, ensuring that it works reliably throughout its usage lifespan. For any builder, understanding these two aspects is essential for producing a high-quality piece of equipment.
Initial Testing Procedures
Once the assembly is complete, conducting initial tests is crucial. Start with a visual inspection of all components to ensure they are properly installed and secured. Check the drive system to confirm that it operates without unusual noises or vibrations. Run the device at low speed to observe how it interacts with the chicken carcass. It is important to monitor for any misalignment of the rubber fingers or inconsistencies in the drum rotation. This phase helps to identify if any adjustments are needed before full operation.
- Visual Check: Examine the entire structure for loose parts.
- Noise Test: Operate the machine at a slow speed and listen for abnormal sounds.
- Rotation Check: Ensure the drum spins evenly without wobbling.
- Finger Alignment: Check that rubber fingers make proper contact with the surface.
Recording observations during this phase can be useful for making necessary adjustments.
Calibrating for Optimal Performance
Once initial tests are complete, calibrating the chicken plucker is the next step. Calibration involves adjusting components to achieve the desired performance. This includes fine-tuning the speed of the drum, the tension of the drive system, and ensuring the rubber fingers are in the correct position for maximum efficiency.
To calibrate effectively:
- Adjust Drum Speed: Experiment with different speeds. Most pluckers operate well between 40-60 RPM. Finding the best speed ensures feathers are removed without damaging the carcass.
- Optimize Finger Spacing: Ensure the rubber fingers are neither too close nor too far apart. Incorrect spacing can lead to ineffective plucking.
- Check Drive System Tension: If the drive belt or chain is too loose or tight, it can affect overall performance. Adjust as necessary.
- Observe During Operation: Continuously monitor performance, adjusting components based on feedback during tests.
Calibrating the chicken plucker not only enhances its efficiency but also extends its lifespan. Therefore, investing time and effort into these processes is not only wise but essential.
Proper testing and calibration ensure that your chicken plucker operates smoothly and effectively, enhancing productivity.
Common Challenges and Solutions
Building a chicken plucker is a satisfying project, but it does come with its set of challenges. Understanding these challenges and having effective solutions can make the building process smoother. Addressing common issues ensures a functional and efficient machine, ultimately leading to better poultry processing results. This section discusses typical problems and provides strategies to overcome them.
Identifying Common Issues
When embarking on the construction of a chicken plucker, builders may face several typical hurdles. Recognizing these issues is the first step in finding a resolution.
Common Issues Include:
- Inefficient Plucking: Sometimes the plucker does not remove feathers completely. This can be due to improper finger placement or inadequate drum speed.
- Mechanical Failures: Breakdowns can occur if components are not securely attached or of low quality. A faulty drive system can halt operations completely.
- Vibration Problems: An unbalanced drum can lead to excessive vibration. This not only affects performance but can also pose safety risks.
- Material Wear and Tear: Continuous use might cause rubber fingers and other components to degrade, leading to reduced efficiency over time.
Identifying these potential pitfalls early allows builders to implement measures to avoid them, enhancing the overall functionality of the chicken plucker.
Effective Troubleshooting Techniques
Once issues are identified, resolving them promptly is crucial. Below are some troubleshooting techniques that can facilitate smoother operation and maintenance of your chicken plucker.
Troubleshooting Tips Include:
- Adjusting the Drum Speed: If feathers are not being removed effectively, experiment with different drum speeds. A higher speed may improve feather removal, but ensure that the rubber fingers do not get damaged.
- Securing Loose Parts: Periodically check for any loose components. Tighten bolts and screws regularly to prevent mechanical failures.
- Balancing the Drum: If vibrations are excessive, it may be necessary to rebalance the drum. Add weights to uneven areas or redistribute existing weights to achieve balance.
- Replacing Worn Components: It is vital to routinely inspect rubber fingers and other key parts for wear. Replace them as needed to maintain performance levels.
- Regular Maintenance: Establish a maintenance schedule. Regular lubrication of moving parts and cleaning can prevent many common issues.
Effective problem identification and troubleshooting not only save time but also enhance the longevity and efficiency of your chicken plucker.
By preparing for these challenges and knowing the solutions, builders can confidently construct a reliable chicken plucker. Such preparation leads to a more satisfying and productive experience in poultry processing.
Maintenance Practices
Maintaining a chicken plucker is critical for ensuring its longevity and efficiency. Over time, wear and tear can affect performance, leading to suboptimal results. Regular maintenance practices help identify issues early and prolong the life of the equipment. It also enhances safety, as malfunctioning parts can pose risks during operation. Therefore, implementing systematic maintenance practices is not just practical but essential for peak performance and safety in poultry processing.
Regular Maintenance Tasks
Regular maintenance tasks are straightforward yet vital. They typically include:
- Cleaning the drum and rubber fingers: Debris can accumulate from use, affecting plucking efficiency. A clean system works better and reduces the risk of bacterial growth.
- Lubricating moving parts: Components such as the drive system require lubrication to function smoothly. This prevents friction and extends the life of the machine.
- Checking the electrical system: For electric pluckers, assessing wires and connections ensures safety and functionality. Any fraying or loose connections should be addressed immediately.
- Inspecting the frame: Ensure that all parts of the pluckerโs frame are tight and secure. Loose bolts or screws can cause instability.
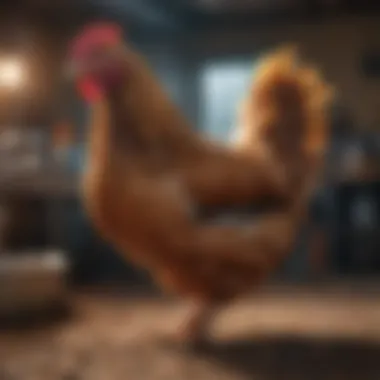
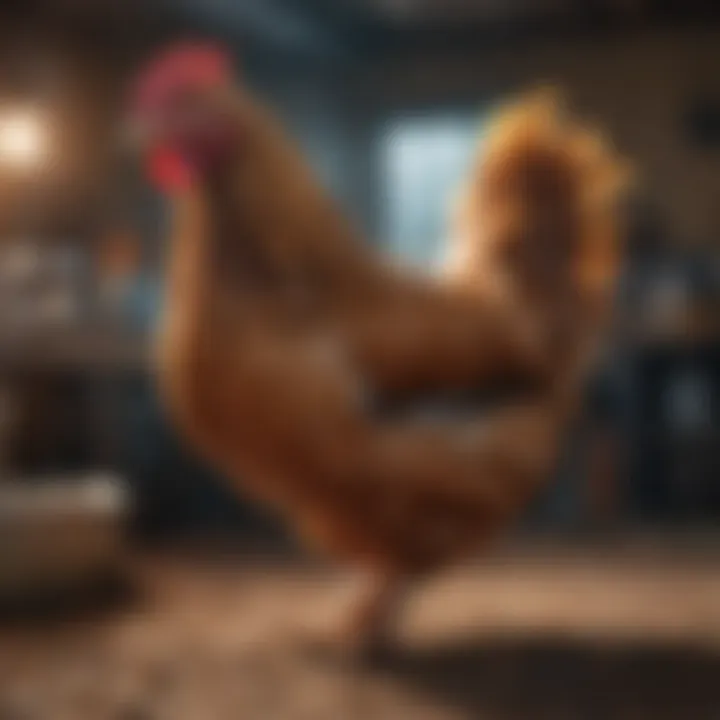
Staying consistent with these tasks allows for smooth operations and saves time and costs in repairs.
Inspecting for Wear and Tear
Wear and tear is inevitable in mechanical systems, and recognizing its signs is crucial. Regular inspections allow builders to catch problems early before they escalate into major issues. Common areas to monitor include:
- Rubber Fingers: These can wear down and lose their ability to effectively pluck feathers. Replace them if you notice any significant damage or loss of flexibility.
- Drum Surface: Over time, the drum can become scratched or dented. Such imperfections can affect the plucking process, leading to inefficiencies. A smooth drum surface is essential for optimal performance.
- Drive System Components: Gears and belts should be inspected for signs of wear. If they show signs of fraying or breaking, it's time to replace them.
- Electrical Connections: Regular visual checks can prevent unexpected failures. Look for rust, corrosion, or loose wires.
Regular inspections reduce downtime and increase productivity. The small time investment in checking components can lead to significant gains in efficiency and safety.
Safety Considerations
When building a chicken plucker, keeping safety at the forefront is critical. The environment in which this equipment operates often involves sharp tools, moving parts, and potentially heavy components. Taking safety seriously helps prevent accidents and ensures that the process remains efficient. In this section, we will look into the risks involved and how to mitigate those risks effectively.
Evaluating Risks Involved
Understanding the various risks is the first step in ensuring safety. There are several key hazards to be aware of when constructing a chicken plucker:
- Sharp Tools: Most of the tools used, such as knives, saws, or wrenches, can cause cuts or lacerations.
- Electrical Hazards: If the plucker is electrically operated, risks related to electric shock also arise. Improper handling of wires or connections can lead to serious injuries.
- Moving Parts: The components in the plucking mechanism operate at high speeds. Keeping fingers or clothing away from such parts is paramount.
- Heavy Components: Lifting or positioning large parts may lead to strains or musculoskeletal injuries.
Mitigating these risks begins with ensuring the workspace is organized and that proper personal protective equipment (PPE) is utilized.
Implementing Safety Measures
Implementing effective safety measures can significantly reduce the likelihood of accidents and injuries during the construction of a chicken plucker. Here are some practical steps to consider:
- Wear Protective Gear: Always wear safety glasses and gloves. Consider steel-toed boots if heavy items are handled frequently.
- Electrical Safety: Ensure that all electrical connections are properly insulated and waterproofed. Use circuit breakers and other equipment designed to minimize electric shock risks.
- Use Proper Tools: Select the right tools for the tasks at hand. This minimizes the need for excessive force and decreases the injury risk.
- Work in Pairs: Having another person present can help monitor safety, especially when lifting heavy objects or operating machinery.
Safety should always be a priority over speed in any construction endeavor.
- Create a Clear Workspace: Keep all tools organized and ensure free movement around the area. Cleaning up spills immediately can prevent slipping or other accidents.
By closely evaluating the risks and taking proactive steps, builders can work more safely and efficiently. This attention to safety not only protects the individual involved but also ensures that the entire process is executed smoothly.
Cost Analysis
Understanding the cost implications of building a chicken plucker is pivotal for both novice and experienced builders. By analyzing costs, individuals can make informed decisions that align with their budgets and project goals. Moreover, a comprehensive cost analysis helps in assessing the feasibility of the project and identifying potential areas for savings. In addition, considering the overall expenses can guide builders in selecting materials and tools that will optimize their investment.
Estimating Total Costs
When estimating total costs, it is essential to account for various factors that contribute to the overall expenditure. Start by listing all necessary materials such as the drum, rubber fingers, and the drive system. Each item should have a projected cost based on current market prices. Also include any additional components that may be needed for assembly.
Labor costs should be considered if individuals plan to hire help. Determine if the project will be a DIY effort or if assistance is necessary. This can affect the overall budget significantly.
Lastly, do not forget about miscellaneous costs such as shipping fees, taxes, and equipment rental, if applicable. Hereโs a breakdown of categories to consider:
- Materials: Prices for components like motors, drums, and rubber fingers.
- Tools: Inventory of tools needed to construct the plucker.
- Labor: Costs associated with professional assistance.
- Miscellaneous: Shipping, taxes, and unexpected expenses.
By taking a detailed approach in estimating total costs, builders can prepare for the financial aspects of the project effectively.
Understanding Return on Investment
Return on investment (ROI) is a crucial metric that provides insight into the potential profitability and advantages of building a chicken plucker. Calculating ROI helps builders evaluate the long-term benefits of their construction.
To determine ROI, consider the savings generated from building a plucker versus purchasing a pre-built model. Factor in the time saved during processing and how effectively a chicken plucker increases productivity. Quantifying these savings allows builders to see tangible returns over time.
Furthermore, builders can project how many chickens will be processed and how this aids in meeting supply demands. This can translate into greater revenue, especially for those in small-scale poultry farming or processing.
Calculating ROI involves the following:
- Initial Cost: Total expenses incurred during the build.
- Value of Savings: Assess the savings compared to store-bought options.
- Projected Revenue: Consider any increase in sales or efficiency gained.
In summary, objectivly analyzing costs and understanding ROI provide valuable insights that support decision-making when building a chicken plucker. These assessments not only ensure financial prudence but also enhance the potential success of poultry processing initiatives.
Finale and Recommendations
The conclusion and recommendations section serves as a significant capstone to the exploration of building a chicken plucker. It reiterates critical insights drawn from the entire article, emphasizing the importance of well-structured poultry processing equipment. The decision to construct a chicken plucker is not just a practical undertaking; it reflects a commitment to efficiency and sustainability in poultry processing.
In this analysis, several essential elements have been discussed. Understanding the mechanisms, materials, and designs of chicken pluckers can influence the effectiveness of construction. The assembly, maintenance, and safety considerations are crucial for a successful build. This section aims to synthesize those insights to provide a clear path forward for builders.
Summary of Key Points
- Chicken pluckers are an essential tool for efficient poultry processing.
- There are various designs available, including vertical and horizontal options, catering to different processing needs.
- Using the right materials and tools is critical to ensure durability and functionality.
- Regular maintenance practices enhance the longevity and efficiency of the machine.
- Safety considerations are paramount when operating plucking machinery.
Building a chicken plucker requires careful planning and execution, ultimately contributing to a more streamlined processing experience.
Future Considerations for Builders
As builders advance in their skills and knowledge, they should consider some key areas:
- Innovation in Design: New technologies may influence future designs of chicken pluckers. Builders might explore features such as automated systems or energy-efficient operations.
- Material Advancements: Utilizing advanced materials can improve the durability and performance of the plucker.
- Community Engagement: Connecting with fellow builders through forums like reddit.com and local workshops can provide valuable insights and tips.
- Sustainability Practices: Looking for eco-friendly options in both building materials and operational methods should be a priority.